Success Story
Vegetable Oil Processor Saves Costs with Dimpleflo Heat Exchangers
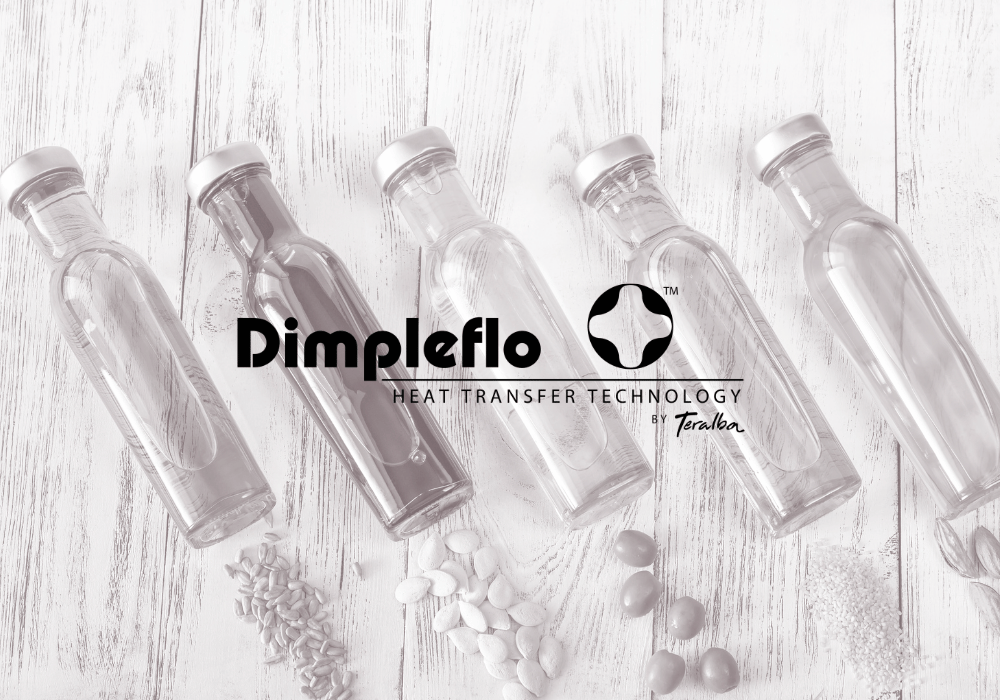
Client Overview
A vegetable oil processing facility located in Marrickville, Sydney, was facing operational and maintenance challenges with its existing Plate Heat Exchanger (PHE). The facility was using this equipment to heat oil with steam, but frequent maintenance and cleaning needs were causing production delays and significant financial strain.
Problem
The plant’s Plate Heat Exchanger was initially performing well, but after a few months of use, it became clogged with residue, slowing down the heat transfer process and disrupting production. Maintenance schedules were difficult to manage, often requiring overtime pay, weekend work, and emergency procurement of replacement parts. Each service involved significant downtime, leading to further delays and increased costs.
Key Challenges:
- Frequent clogging and inefficient heat transfer
- High maintenance costs due to emergency parts and labor
- Production delays caused by downtime
- Increased energy usage and steam waste
Solution Provided
Dimpleflo’s Unique Heat Exchanger Technology: Teralba engineers were called in to assess the situation and propose a solution that would eliminate the costly maintenance cycles. After carefully reviewing the plant’s requirements, flow rates, and heating needs, Teralba recommended installing a Dimpleflo Monotube Heat Exchanger. This model was chosen due to its ability to create enough turbulence using the unique dimple profile design, which prevents fouling and keeps heat transfer surfaces clean without regular maintenance.
Key Solutions:
- Optimised Dimpleflo tube sizing for maximum efficiency
- Monotube Design to Minimize Fouling and Maximize Heat Transfer
- A Steam Manifold System to Ensure Optimal Steam Use
- Integrated Condensate Drainage to Prevent Steam Stalls
- Modular Configuration for Easy Installation in a Cramped Facility
Implementation
Due to the constraints of the plant’s layout, Teralba designed a modular system, which allowed the heat exchanger to be brought in as smaller units and assembled on-site with millimeters of clearance. This approach minimized disruption and allowed the facility to continue operations with minimal downtime.
Timeline
The installation and commissioning were completed within 3 days, getting the plant back online promptly.
Innovation
The modular system design enabled the exchanger to fit within the tight space, demonstrating Teralba’s ability to customize solutions for challenging environments.
Results
A vegetable oil processing facility located in Marrickville, Sydney, was facing operational and maintenance challenges with its existing Plate Heat Exchanger (PHE). The facility was using this equipment to heat oil with steam, but frequent maintenance and cleaning needs were causing production delays and significant financial strain.
Maintenance Costs Eliminated
The Dimpleflo system required no cleaning or rebuilds, eliminating the need for costly emergency maintenance.
Energy Efficiency
Steam usage decreased significantly, leading to substantial energy savings.
Increased Production Efficiency
With no clogging or downtime, the production process ran smoothly, improving overall output.
Fast Return on Investment
The savings from reduced maintenance and energy costs meant that the system paid for itself within a short period.
Conclusion
The implementation of the Dimpleflo Heat Exchanger not only solved the immediate issues of high maintenance costs and production delays but also provided long-term efficiency improvements. The client experienced significant cost reductions and operational benefits, leading to a more streamlined process and better energy utilization.
Explore Other Success Stories with Dimpleflo™
Increasing Efficiency at an Australian Food Manufacturing Plant with Dimpleflo Heat Exchangers
Success Story Increasing Efficiency at an Australian Food Manufacturing Plant with Dimpleflo Heat Exchangers Simplot Australia Simplot Australia is a...
Read MoreSydney Linen Cleaning Company Saves Big with Dimpleflo
Success Story Sydney Linen Cleaning Company Saves Big with Dimpleflo Client Overview A Sydney-based linen cleaning company processes 45 tonnes...
Read MoreReady to Transform Your Operations?
Let Dimpleflo™ help you optimise your heat transfer processes for increased efficiency, cost savings, and superior performance.