Dimpleflo™
35 Years of Innovation and Excellence
Dimpleflo™ Difference
Dimpleflo™ Heat Exchangers are ideal for heating and cooling of viscous and fouling fluids. The Dimple profile induces turbulence deep into the fluid flow which increases Reynolds numbers. The coefficient of heat transfer increase as a result of Dimpleflo tubing is greater than the pressure drop penalty giving Dimpleflo a great return on investment.
Dimpleflo can withstand high pressures and temperatures in many cases beyond smooth tubing.
Dimpleflo™ profiles can be tailored to each application to optimise the rate of heat transfer.
Features
Enhanced Fluid Turbulence
Dimpled tubing creates turbulence and high Reynolds numbers in the fluid flow.
High-Pressure Capability
Suits high pressure applications up to 25 bar - internal tube design.
High-Temperature Performance
Suits use with steam and high temperatures up to 250 degreesC.
Versatile Fluid Handling
Suitable for heating and cooling of any pumpable fluid.
Custom Dimple Configurations
Varying Dimple Design Combinations for Specific Duties.
Space-Saving Compact Design
Existing heat exchangers han be re-tubed with Dimpleflo tubing and achieve up to 50% additional capacity in the same shell or footprint.
Dimpleflo TM Profile Range
Profiles are altered depending on the application for which the heat exchanger is used in.
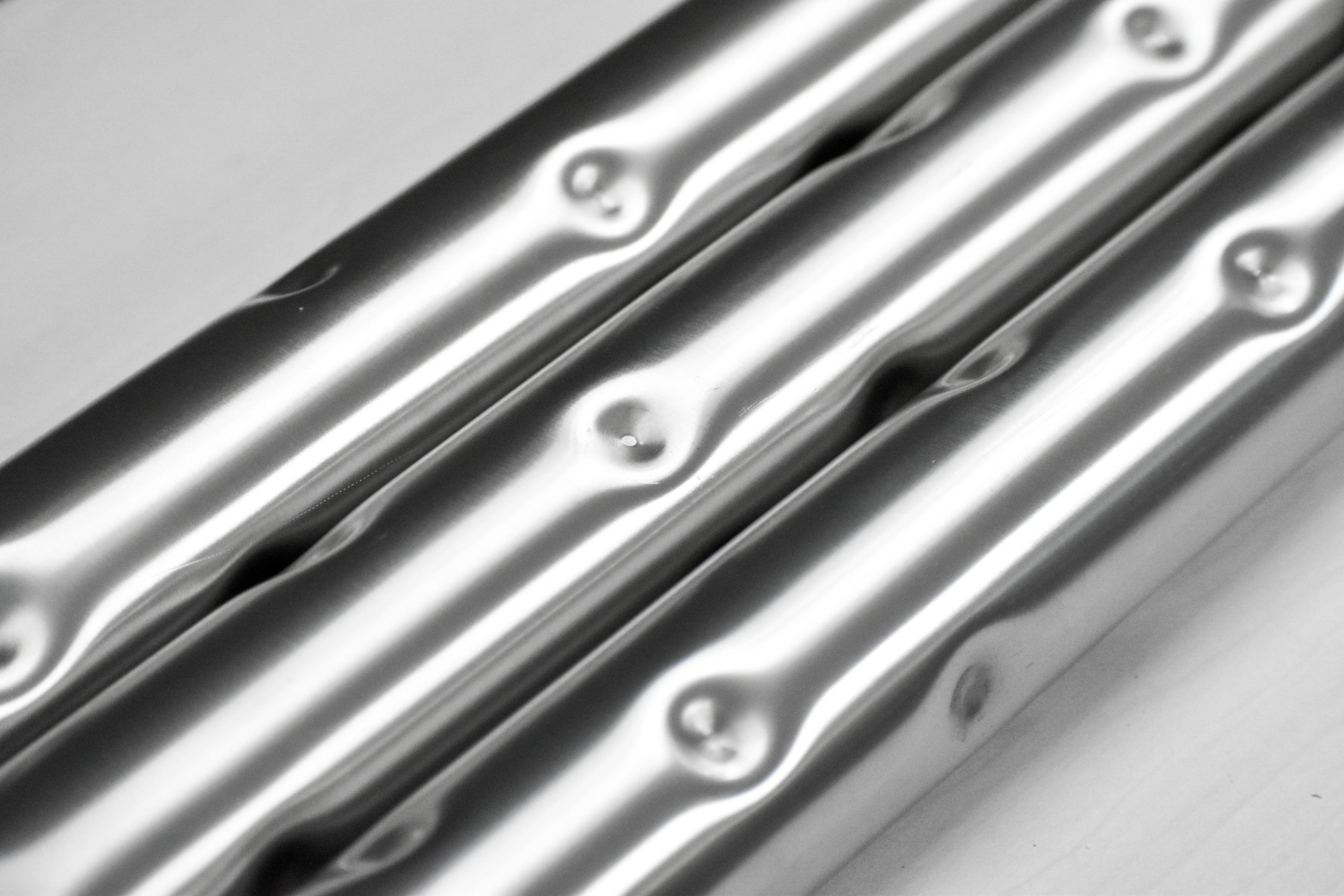
Shallow Dimple Profile
Used in applications for gases and vapours.
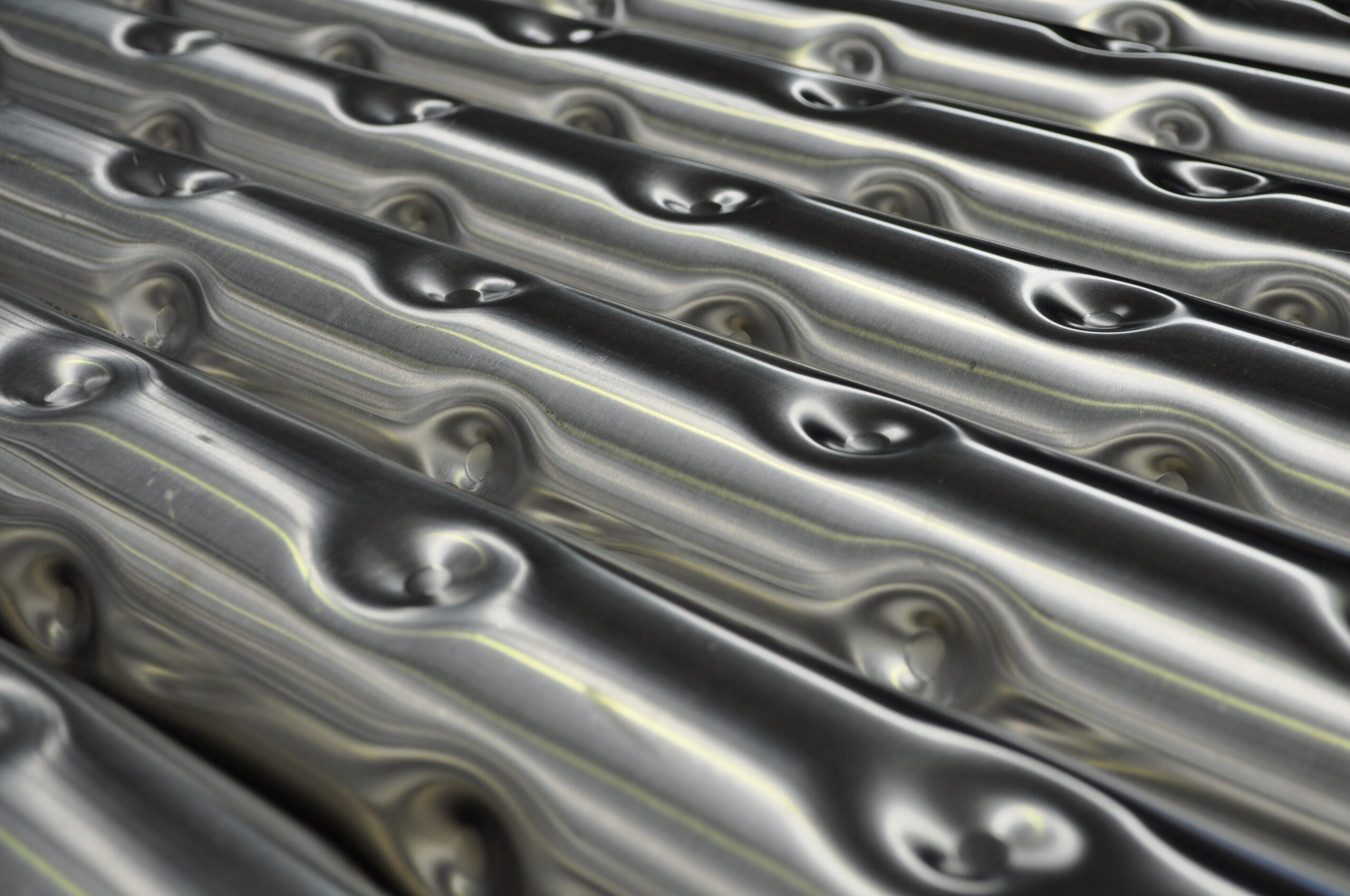
Standard Profile Range
Used in applications for water, oil and service fluids.

Heavy Profile Range
Used in applications for viscous and fouling fluids.
Options for Usage
Sewage Heating
Heating or cooling municipal sewage to maintain optimum temperatures in sewage digesters.
Energy Recovery
Energy recovery from hot waste water or greasy effluents to satisfy EPA requirements and reclaim.
Evaporation
Evaporation processes to concentrate liquids or remove moisture in various industrial applications.
Condensing
Condensing vapor into liquid, used in heat recovery and refrigeration systems for efficient thermal management.
Oil and Gas
Specialised heat exchangers for the oil and gas industry, managing extreme temperatures and pressures in extraction and refining processes.
Viscous Fouling Fluids
Heat exchangers designed for handling viscous fluids prone to fouling, ensuring reliable operation in heavy-duty industrial processes.
In Application
Discover how Dimpleflo™ technology is applied across different sectors, enhancing performance and efficiency.
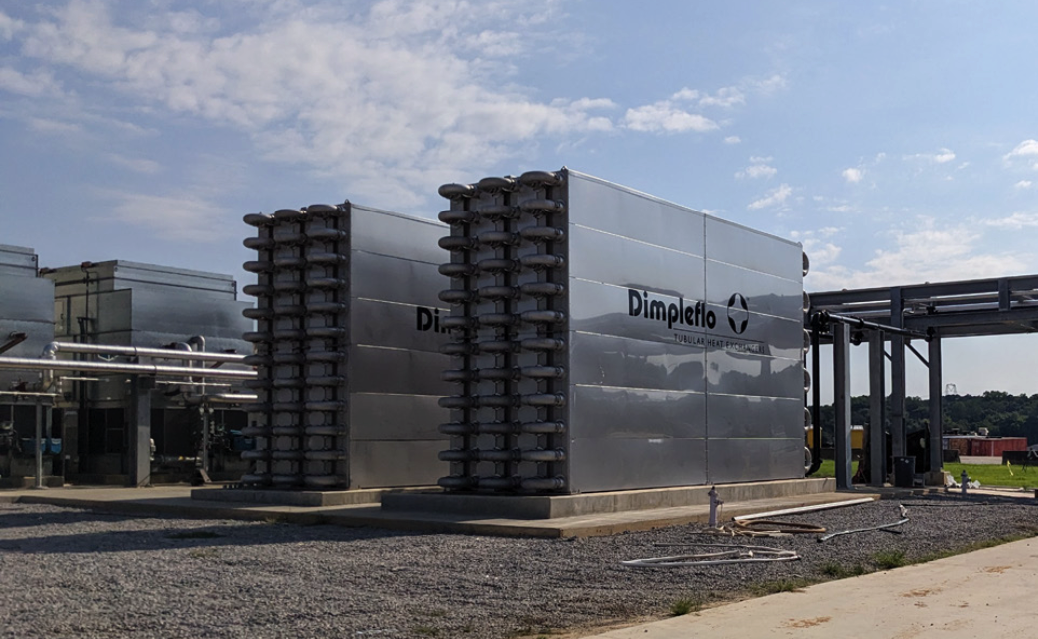
Two 72T 168 219 9000 I MAN Dimpleflo units used to cool biomass after heat treatment, ready for processing in huge digesters.
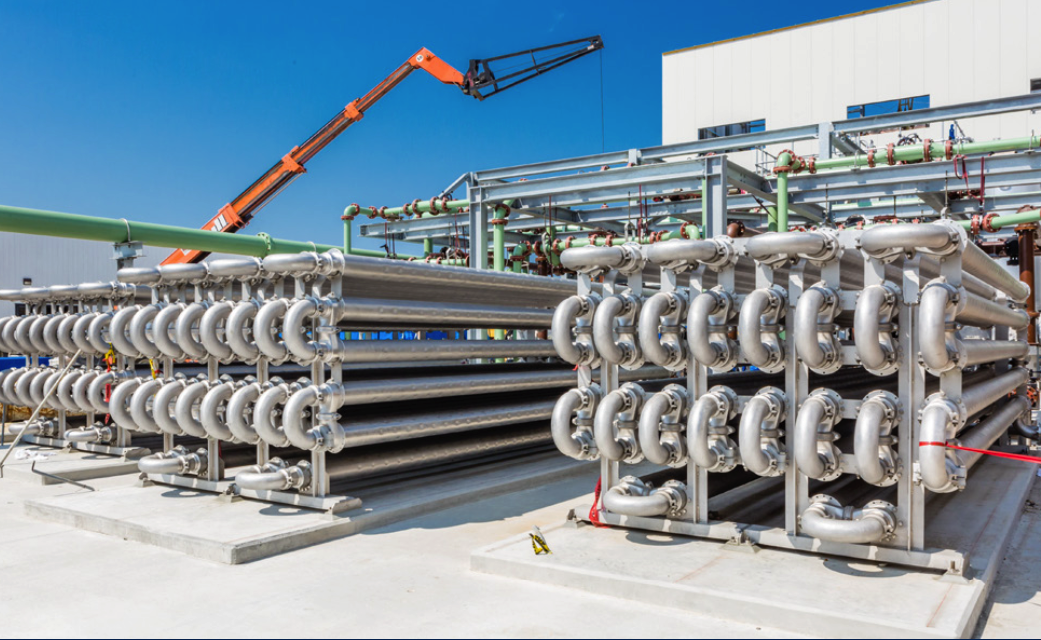
Two duty and one standby Dimpleflo heat exchangers used for cooling THP Sludge in a new technology treatment plant.

Dimpleflo heat exchanger with a closed circuit cooling loop for processing up to 80% solids.
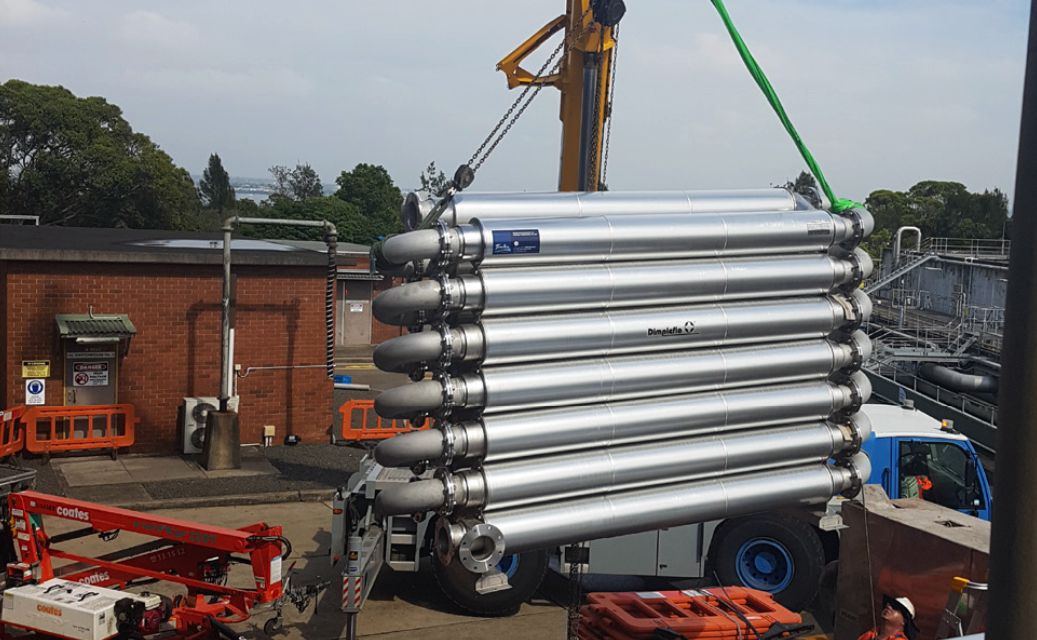
Dimpleflo installation for traditional sludge heating in an anaerobic digestor.
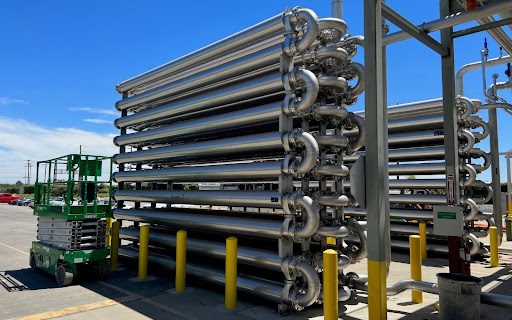
Design and manufacture of an additional must chiller unit for installation in a large California winery.
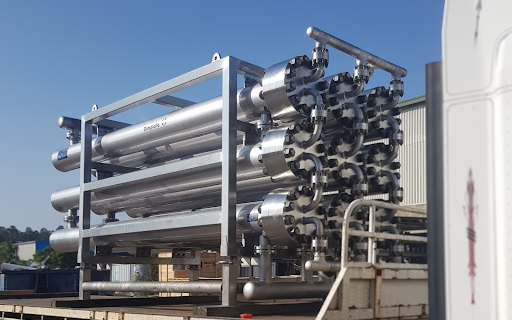
Design and manufacture of 2 x containerised heat exchangers capable of operating at high temperature and extreme pressure.
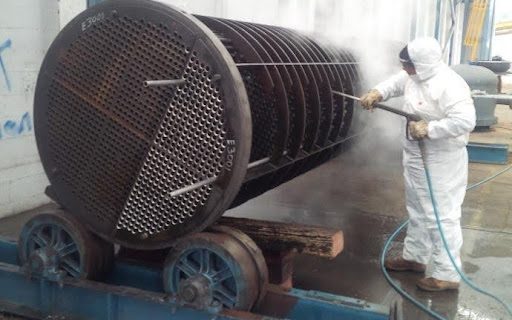
Dimpleflo shell and tube heat exchanger replacement of a plate heat exchanger in a viscous, fouling application.
CFD Video
Tube Dimpling Video
Tube Dimpling Video
Success Stories
Increasing Efficiency at an Australian Food Manufacturing Plant with Dimpleflo Heat Exchangers
Success Story Increasing Efficiency at an Australian Food Manufacturing Plant with Dimpleflo Heat Exchangers Simplot Australia Simplot Australia is a...
Read MoreSydney Linen Cleaning Company Saves Big with Dimpleflo
Success Story Sydney Linen Cleaning Company Saves Big with Dimpleflo Client Overview A Sydney-based linen cleaning company processes 45 tonnes...
Read MoreVegetable Oil Processor Saves Costs with Dimpleflo Heat Exchangers
Success Story Vegetable Oil Processor Saves Costs with Dimpleflo Heat Exchangers Client Overview A vegetable oil processing facility located in...
Read MoreDimpleflo™
35 Years in the Making
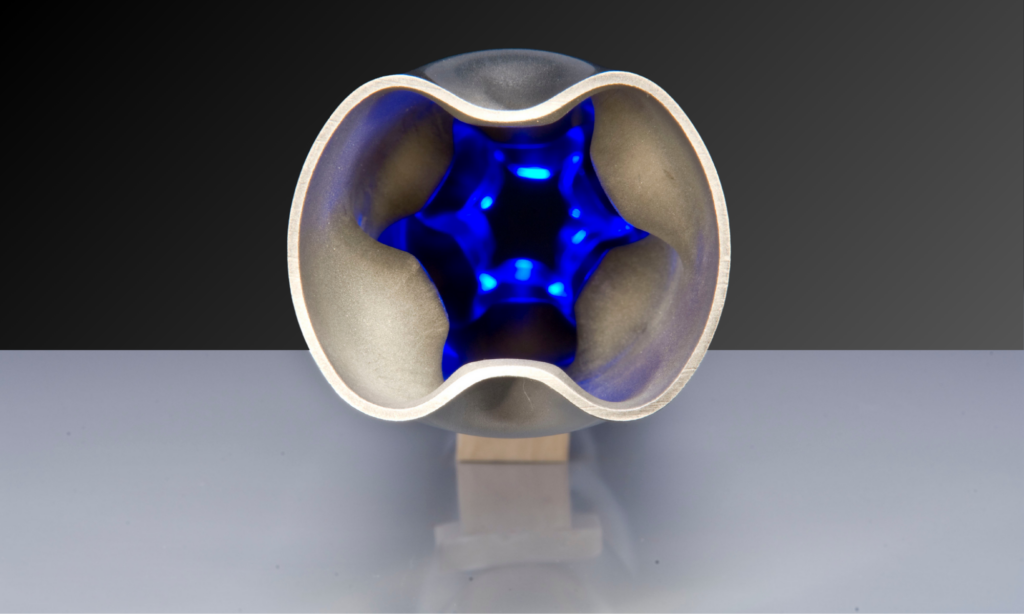
Our Journey
Discover how our milestones have shaped who we are today.
Dimpleflo began with an idea, some prototypes and a series of heat transfer tests. With the product showing definite efficiency gains over plain tube, the inventor commissioned a PhD qualified chemical engineer, who built a heat transfer selection program that ran on Apple 2E computer.
Dimpleflo began with an idea, some prototypes and a series of heat transfer tests. With the product showing definite efficiency gains over plain tube, the inventor commissioned a PhD qualified chemical engineer, who built a heat transfer selection program that ran on Apple 2E computer.
Why Choose Dimpleflo™ for Your Heat Exchanger Needs?
When it comes to heat transfer solutions, Dimpleflo™ stands out for its innovation, efficiency, and tailored approach. Our custom-designed heat exchangers are built specifically to meet the demands of your industry. With over 35 years of expertise, we offer quick turnaround times, expert support, and energy-efficient designs that save costs while delivering reliable performance.
Partner with us to experience industry-leading technology and personalised solutions that ensure your success.
Turbulence-Enhanced Heat Transfer Efficiency
Dimpleflo™ heat exchangers use a revolutionary dimpled tube design that enhances turbulence, significantly improving heat transfer efficiency by up to 30% without increasing pressure drop.
Smaller, More Compact Heat Exchanger Designs
By optimising the heat transfer process, Dimpleflo™ reduces the overall length of the heat exchanger, resulting in more compact, space-saving designs that save valuable plant space.
Energy Savings and Cost Reduction
The efficiency gains from Dimpleflo™ lead to reduced energy consumption, saving companies up to 25% on pumping energy and significant cost savings over time.
Anti-Fouling Self-Cleaning Mechanism
The turbulence generated by the dimpled design acts as a self-cleaning mechanism, preventing fouling and reducing the need for frequent shutdowns and maintenance.
Sustainability and Environmental Impact
Dimpleflo’s design reduces energy consumption and lowers CO2 emissions, contributing to long-term sustainability and supporting environmental goals.
Customised Solutions for Specific Industry Needs
Dimpleflo™ heat exchangers are customised to meet the specific requirements of industries like food processing, chemicals, and power generation, ensuring optimal performance for each application.
Faster Return on Investment (ROI)
Due to energy savings, reduced fouling, and minimised downtime, Dimpleflo™ systems offer a faster return on investment, helping companies recoup costs more quickly.
Long-Term Reliability and Reduced Downtime
Dimpleflo’s enhanced efficiency and anti-fouling properties result in fewer shutdowns and maintenance, increasing system reliability and keeping operations smooth.
Proven Expertise and Industry Innovation
With over 35 years of experience and a history of innovation, Dimpleflo™ is a trusted leader in heat transfer solutions, delivering high-performance systems for demanding industrial applications.
Frequently Asked Questions
Find quick answers to common inquiries about our products, services, and technical specifications to help you make informed decisions with ease.
Any more questions? Please contact us.
What industries can Dimpleflo™ heat exchangers be used in?
Dimpleflo™ heat exchangers are versatile and can be applied across various industries, including food processing, wastewater treatment, chemical processing, biopharmaceuticals, energy recovery and other heavy industries. They are especially effective in handling viscous and particulate-laden fluids.
What are the main advantages of Dimpleflo™ heat exchangers?
Dimpleflo™ heat exchangers offer numerous benefits, such as:
- Enhanced fluid turbulence: The dimpled tube design increases turbulence for improved heat transfer.
- High-pressure and high-temperature capability: Suitable for use in applications with pressures up to 25 bar and temperatures up to 250°C.
- Minimal maintenance: The single fluid flow path prevents blockages and reduces the need for costly maintenance.
- Compact and modular designs: Space-saving and allows for future expansion.
Can Dimpleflo™ heat exchangers handle fouling fluids?
Yes, the dimple profiles create a turbulent flow that prevents fouling by keeping particles in suspension. This makes Dimpleflo™ heat exchangers ideal for handling viscous fluids, sludges, and slurries.
What is the typical payback time for Dimpleflo™ heat exchangers?
Due to their efficiency and energy-saving capabilities, many Dimpleflo™ heat exchangers have a return on investment (ROI) of less than 12 months, as seen in numerous case studies.
How customisable are Dimpleflo™ heat exchangers?
Dimpleflo™ heat exchangers are highly customizable. Our engineers configure each unit to meet specific client requirements, including fluid type, flow rate, and operating conditions. We also offer various dimple design combinations tailored for specific heat transfer duties.
Can Dimpleflo™ heat exchangers be used for energy recovery?
Yes, Dimpleflo™ heat exchangers are ideal for energy recovery applications, such as recovering heat from hot waste streams or greasy effluents, which can then be reused, reducing energy costs and complying with environmental regulations.
How does Dimpleflo™ technology improve heat transfer efficiency?
The dimpled tube design increases turbulence within the fluid flow, which disrupts boundary layers and enhances heat transfer. This design ensures optimal performance even in high-viscosity or fouled fluids.
Are Dimpleflo™ heat exchangers suitable for high-pressure applications?
Yes, Dimpleflo™ heat exchangers are designed to withstand high pressures of up to 25 bar, making them suitable for demanding industrial processes.
What maintenance is required for Dimpleflo™ heat exchangers?
Thanks to their robust design and turbulence-inducing dimple profiles, Dimpleflo™ heat exchangers require minimal maintenance. Their design prevents blockages and fouling, reducing downtime and associated maintenance costs.
How does Dimpleflo™ handle temperature-sensitive processes?
Dimpleflo™ heat exchangers can handle high temperatures of up to 250°C and are designed for precise temperature control, making them suitable for sensitive processes like biopharmaceutical temperature management and sludge pasteurization.