Dimpleflo™
Industrial Heat Exchanger Technology
Engineered for efficiency and durability, Dimpleflo™ heat exchanger technology delivers high thermal performance across demanding industrial applications—optimising energy use while reducing maintenance and operational costs.
Dimpleflo™ Heat Exchanger Technology
INDUSTRIAL APPLICATIONS
Dimpleflo™ is designed to handle the toughest industrial conditions, delivering superior heat transfer efficiency, reliability, and easy maintenance. Its innovative design makes it ideal for a wide range of applications, including food processing, pharmaceuticals, chemicals, and heavy industries such as wastewater treatment, oil and gas, mining, energy, and marine industries.
Oil and Gas
Mining
Energy
Chemical
Marine
Waste Water
Oil and Gas
Mining
Energy
Chemical
Marine
Waste Water
Dimpleflo™ Profile Range
The Dimpleflo™ heat exchanger range is available in various dimple profiles, each designed to suit specific fluid types and processing conditions. This flexibility ensures optimal thermal performance and operational efficiency across a wide range of industrial applications.
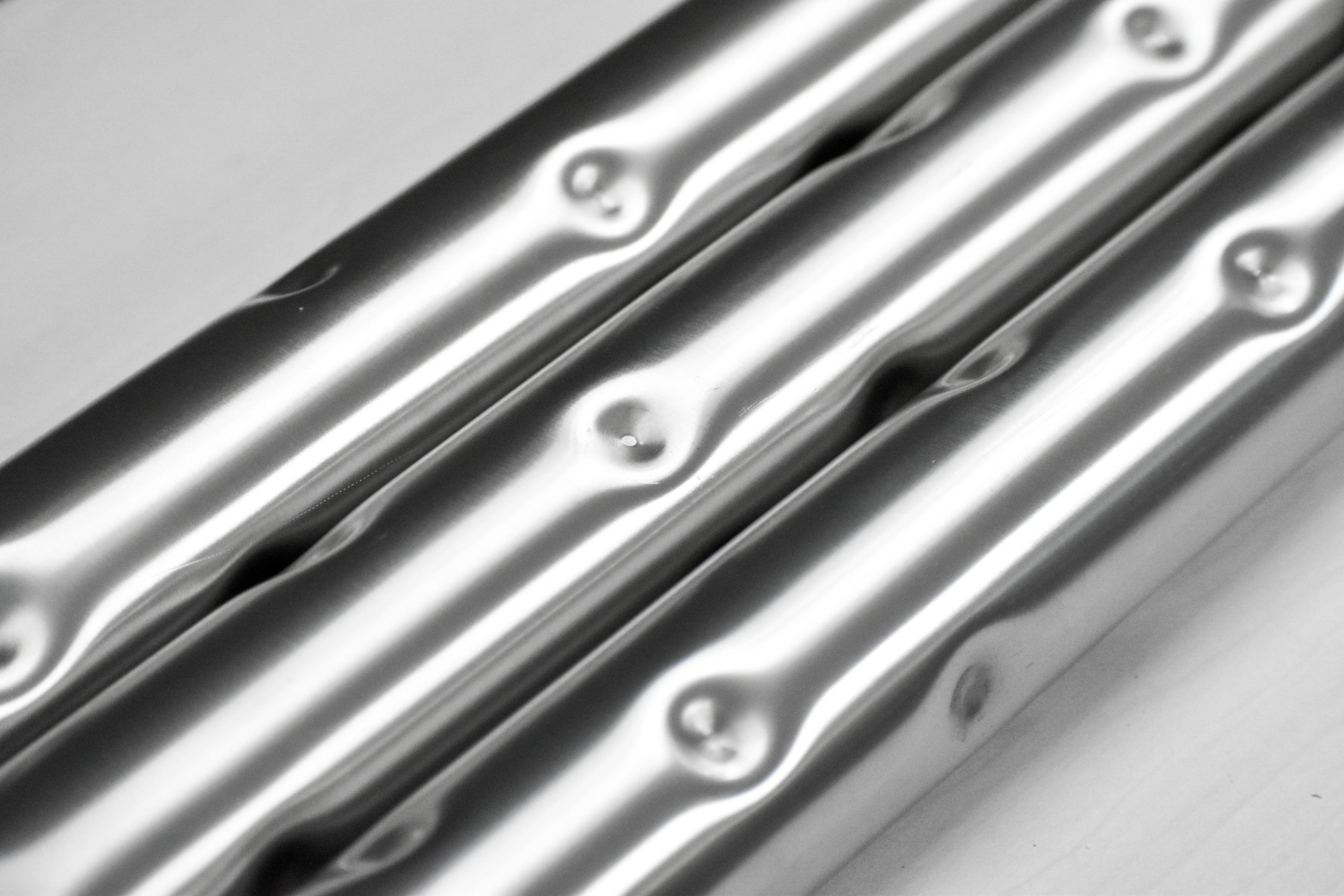
Shallow Dimple Profile
Ideal for low-density media such as gases and vapours, offering efficient heat transfer with minimal pressure drop.
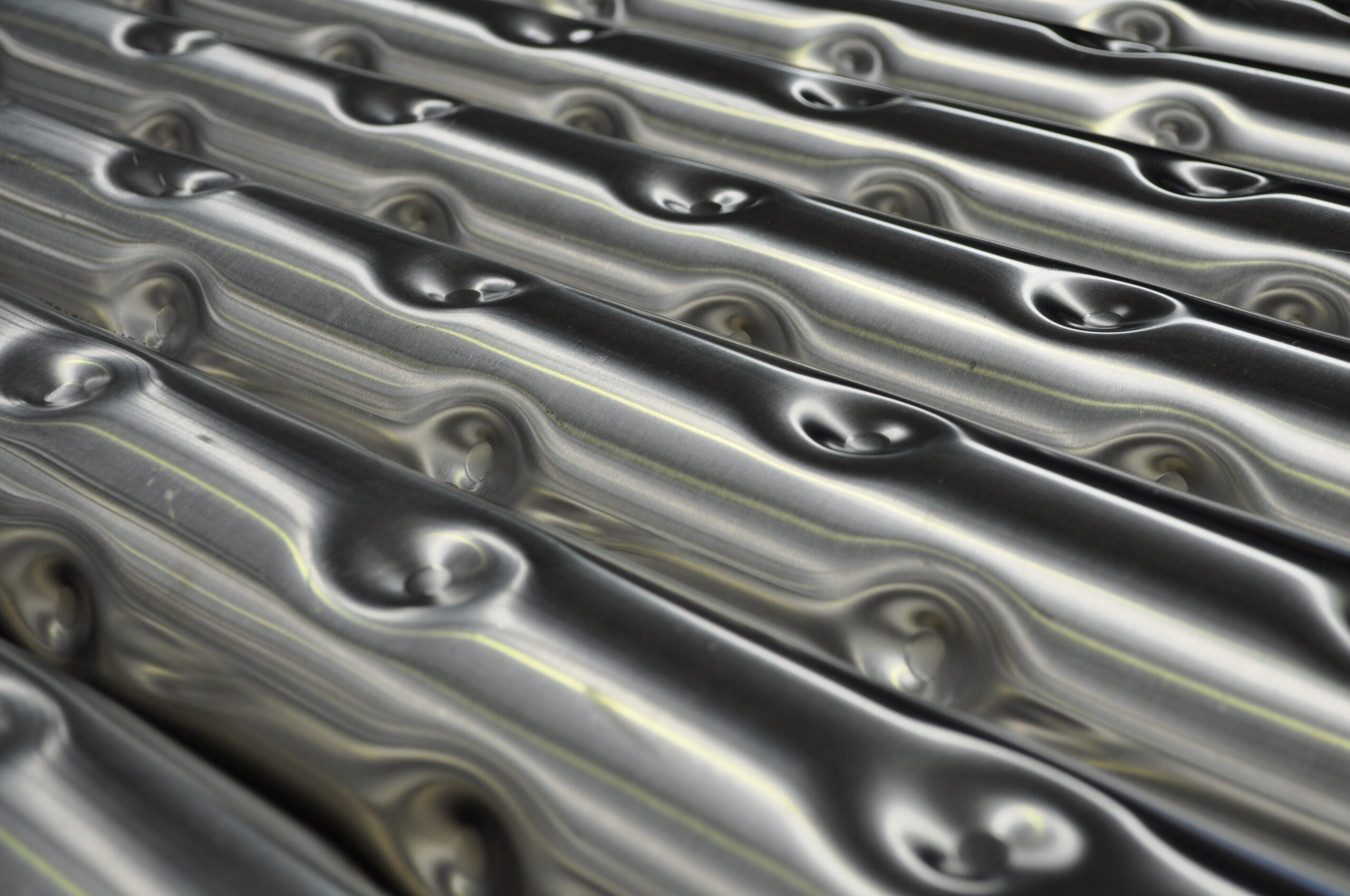
Standard Profile Range
The standard profile, best suited for water, oil, and other service fluids, providing a balance of flow and heat transfer performance.

Heavy Profile Range
Designed for high-viscosity or fouling fluids, this profile ensures robust performance and easy cleaning in demanding process environments.
Dimpleflo™ Heat Exchanger Technology
Features & Capabilities
Dimpleflo™ is engineered for high performance and durability in demanding industrial applications. Its unique dimpled tube design enhances fluid dynamics, allowing for greater heat transfer efficiency, compact installation, and flexibility across a wide range of processes.
Enhanced Fluid Turbulence
The dimpled surface promotes turbulent flow and high Reynolds numbers, significantly improving heat transfer rates.
High-Pressure Capability
Designed to withstand internal pressures of up to 25 bar, making it ideal for demanding process conditions.
High-Temperature Performance
Handles high-temperature applications, including steam, withstanding up to 250°C.
Versatile Fluid Handling
Compatible with the heating and cooling of any pumpable fluid—ideal for diverse industrial applications.
Custom Dimple Configurations
Varying Dimple Design Combinations for Specific Duties.
Space-Saving Compact Design
Existing heat exchangers han be re-tubed with Dimpleflo tubing and achieve up to 50% additional capacity in the same shell or footprint.
Enhanced Fluid Turbulence
The dimpled surface promotes turbulent flow and high Reynolds numbers, significantly improving heat transfer rates.
High-Pressure Capability
Designed to withstand internal pressures of up to 25 bar, making it ideal for demanding process conditions.
High-Temperature Performance
Handles high-temperature applications, including steam, withstanding up to 250°C.
Versatile Fluid Handling
Compatible with the heating and cooling of any pumpable fluid—ideal for diverse industrial applications.
Custom Dimple Configurations
Varying Dimple Design Combinations for Specific Duties.
Space-Saving Compact Design
Existing heat exchangers han be re-tubed with Dimpleflo tubing and achieve up to 50% additional capacity in the same shell or footprint.
CFD Video
Dimpleflo™ Heat Exchanger Technology
Boost Manufacturing and Industrial Processes Efficiency with Smarter Heat Exchange
In heavy industry, improving efficiency goes far beyond saving time—it’s a strategic move that impacts every part of operations. From increasing production output and reducing energy consumption to maintaining consistent quality and meeting strict compliance standards, process efficiency plays a crucial role in long-term success. Companies that optimise their thermal systems gain a competitive edge by lowering operating costs, extending equipment life, and maximising uptime.
Introducing Dimpleflo™ Heat Exchanger Technology
This is where Dimpleflo™ Heat Exchanger Technology steps in. Designed with the realities of modern industrial environments in mind, Dimpleflo™ provides a smarter, more effective way to manage heat transfer. Its unique dimpled tube design creates turbulence within the fluid, significantly increasing heat transfer rates without raising pressure drop. This leads to faster thermal response, improved process control, and better use of plant energy—without the maintenance burden often associated with traditional heat exchangers.
Engineered for Tough Industrial Conditions
Dimpleflo™ is built to handle the toughest conditions. Whether you’re working with high-temperature steam, abrasive slurries, chemical-laden fluids, or heavy sludge, Dimpleflo™ performs with consistent reliability. It operates efficiently at high pressures and temperatures, resists fouling, and is easy to clean—minimising downtime while ensuring stable performance over time. This makes it ideal for industries like mining, oil and gas, wastewater treatment, food processing, energy, and chemicals.
A Smarter Investment in Process Optimisation
Ultimately, Dimpleflo™ isn’t just a heat exchanger—it’s a long-term investment in process optimisation. Improving thermal efficiency and reducing operational headaches empowers facilities to run smoother, safer, and more profitably. For industrial leaders seeking a solution that adapts to demanding conditions while delivering measurable improvements, Dimpleflo™ stands out as the trusted choice for next-generation heat exchanger performance.
Introducing Dimpleflo™ Heat Exchanger Technology
This is where Dimpleflo™ Heat Exchanger Technology steps in. Designed with the realities of modern industrial environments in mind, Dimpleflo™ provides a smarter, more effective way to manage heat transfer. Its unique dimpled tube design creates turbulence within the fluid, significantly increasing heat transfer rates without raising pressure drop. This leads to faster thermal response, improved process control, and better use of plant energy—without the maintenance burden often associated with traditional heat exchangers.
Engineered for Tough Industrial Conditions
Dimpleflo™ is built to handle the toughest conditions. Whether you’re working with high-temperature steam, abrasive slurries, chemical-laden fluids, or heavy sludge, Dimpleflo™ performs with consistent reliability. It operates efficiently at high pressures and temperatures, resists fouling, and is easy to clean—minimising downtime while ensuring stable performance over time. This makes it ideal for industries like mining, oil and gas, wastewater treatment, food processing, energy, and chemicals.
A Smarter Investment in Process Optimisation
Ultimately, Dimpleflo™ isn’t just a heat exchanger—it’s a long-term investment in process optimisation. Improving thermal efficiency and reducing operational headaches empowers facilities to run smoother, safer, and more profitably. For industrial leaders seeking a solution that adapts to demanding conditions while delivering measurable improvements, Dimpleflo™ stands out as the trusted choice for next-generation heat exchanger performance.
In Application
Dimpleflo™ heat exchangers are used in a wide range of real-world industrial applications where durability, efficiency, and high thermal performance are essential. Their adaptability makes them ideal for demanding processes involving sludge, slurry, and high-solid content fluids, as well as environments requiring precise temperature control and minimal maintenance.
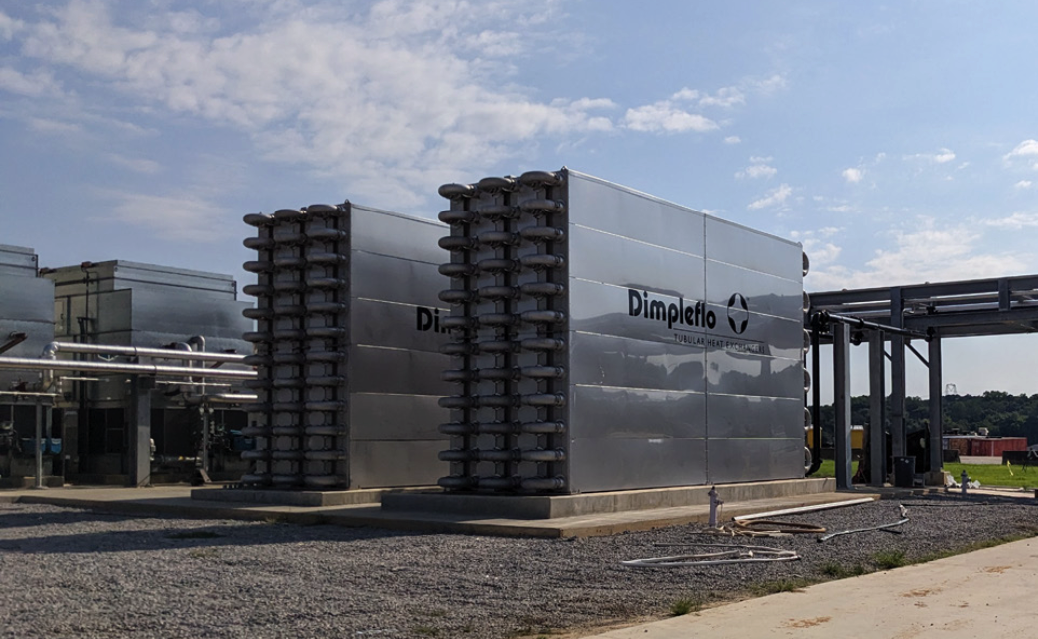
Two 72T 168 219 9000 I MAN Dimpleflo units used to cool biomass after heat treatment, ready for processing in huge digesters.
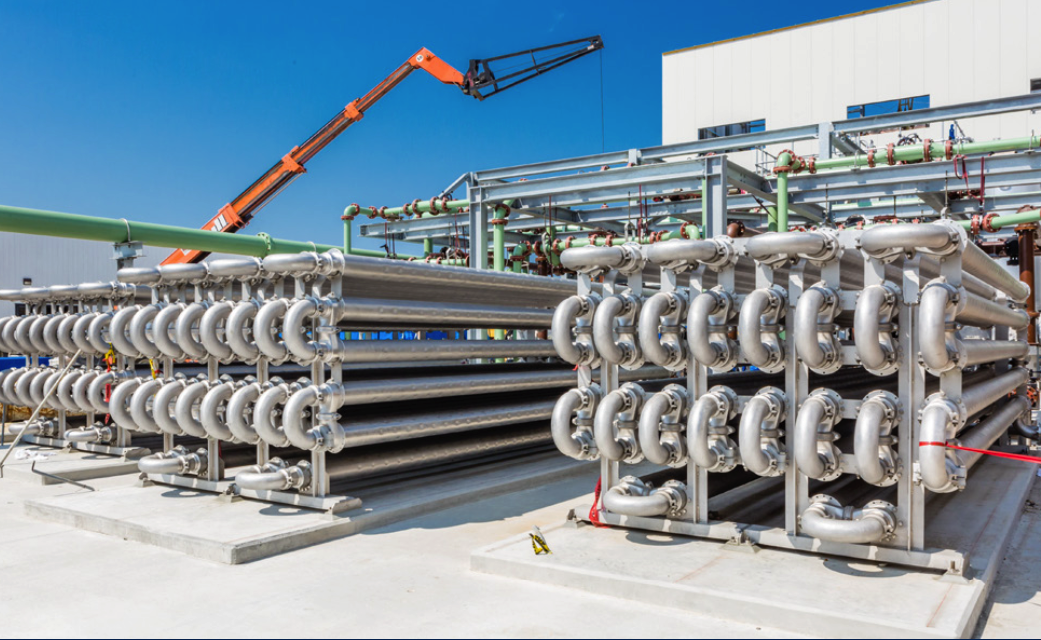
Two duty and one standby Dimpleflo heat exchangers used for cooling THP Sludge in a new technology treatment plant.

Dimpleflo heat exchanger with a closed circuit cooling loop for processing up to 80% solids.
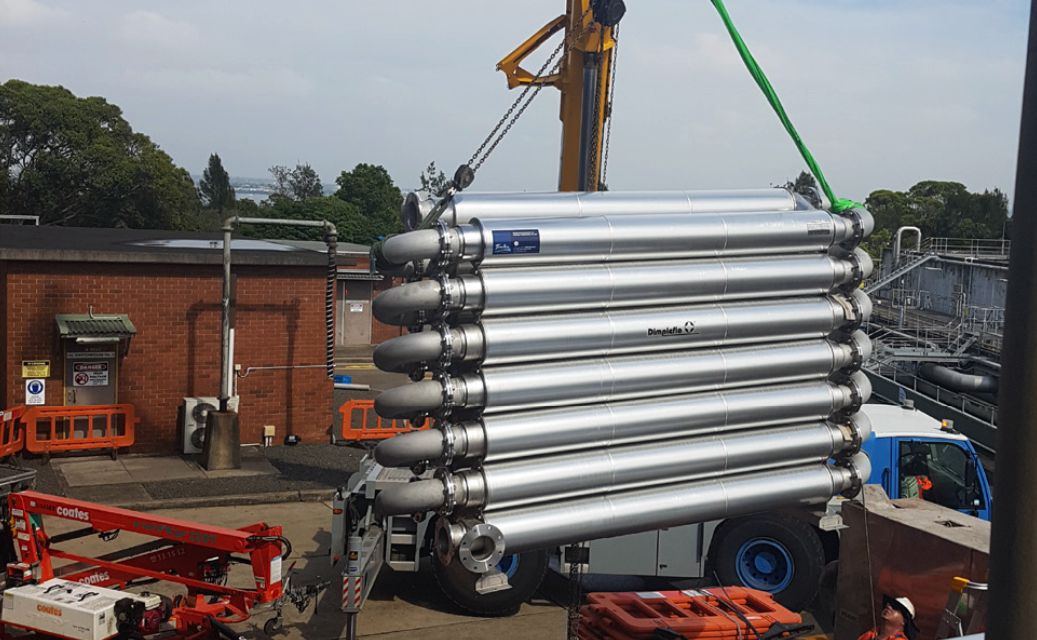
Dimpleflo installation for traditional sludge heating in an anaerobic digestor.
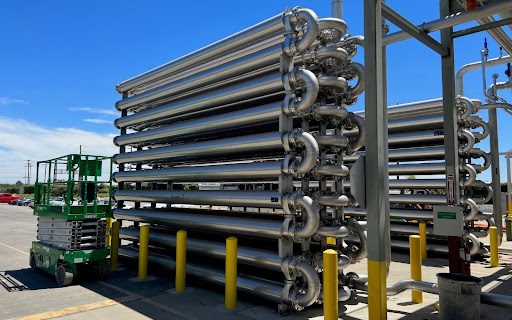
Design and manufacture of an additional must chiller unit for installation in a large California winery.
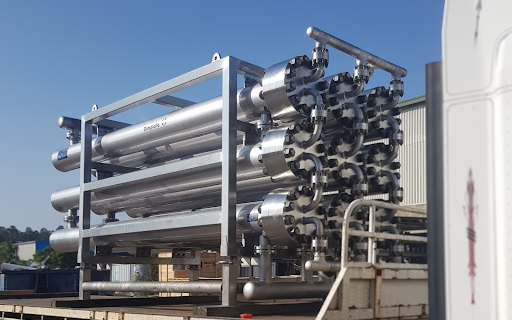
Design and manufacture of 2 x containerised heat exchangers capable of operating at high temperature and extreme pressure.
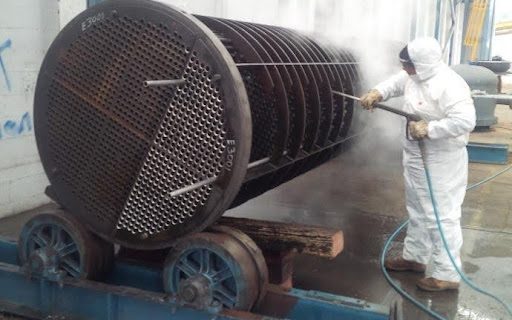
Dimpleflo shell and tube heat exchanger replacement of a plate heat exchanger in a viscous, fouling application.
Tube Dimpling Video
Here’s a quick behind-the-scenes glimpse into our dimpling process. Take a look at Dimpleflo® heat transfer enhancement technology being formed on large diameter Duplex alloy pipes.
Frequently Asked Questions
Find quick answers to common inquiries about our products, services, and technical specifications to help you make informed decisions with ease.
Any more questions? Please contact us.
What is a heat exchanger and how does it work?
A heat exchanger is a device that transfers heat between two or more fluids without mixing them. It works by allowing heat to pass through a solid barrier (like tubes or plates), enabling energy exchange between hot and cold streams while maintaining separation.
What are the main types of industrial heat exchangers?
The most common types include shell and tube, plate, air-cooled, and double pipe heat exchangers. Each type has specific advantages depending on the application, fluid type, pressure, temperature, and maintenance requirements.
How do I know which heat exchanger is right for my industrial process?
Selecting the right heat exchanger depends on several factors: the type of fluid, temperature and pressure requirements, flow rates, space constraints, and fouling potential. A thermal engineer can assess these variables to recommend the best design and configuration.
How does fouling affect heat exchanger performance?
Fouling occurs when unwanted deposits (like scale, sludge, or biofilms) build up inside the exchanger, reducing heat transfer efficiency and increasing pressure drop. Dimpleflo™ helps mitigate fouling with its turbulence-enhancing tube design, which keeps flow paths cleaner over time.
Can heat exchangers be used for both heating and cooling?
Yes. Industrial heat exchangers are designed to either heat or cool process fluids, depending on system needs. The same unit can even perform both functions in different stages of a process, depending on flow direction and configuration.
How often should industrial heat exchangers be cleaned or serviced?
Cleaning frequency depends on the fluid properties and operating environment. For high-fouling applications, regular inspection is recommended. Dimpleflo™ requires less frequent cleaning thanks to its self-scouring design, but maintenance intervals should still be planned based on usage.
What materials are used in industrial heat exchanger construction?
Materials vary based on application and chemical compatibility. Common materials include stainless steel, carbon steel, titanium, and special alloys. Dimpleflo™ is available in a range of materials to match the corrosion resistance and strength your process requires.
How does dimpled tube technology improve heat transfer?
The dimples disrupt the laminar boundary layer along the tube wall, creating localized turbulence. This increases the Reynolds number and enhances thermal efficiency—particularly in fluids with low flow velocities or high viscosity.
What makes Dimpleflo™ different from conventional heat exchangers?
Dimpleflo™ uses patented dimpled tube technology to create higher fluid turbulence, which improves heat transfer efficiency without requiring more energy. It also reduces fouling and supports high-pressure, high-temperature applications.
What industries use Dimpleflo™ heat exchangers?
Dimpleflo™ is used in a wide range of industries including wastewater treatment, mining, oil and gas, chemical processing, energy generation, and food manufacturing. It’s ideal for handling viscous, abrasive, or fouling fluids.
Can Dimpleflo™ be retrofitted into existing systems?
Yes. Dimpleflo™ heat exchangers are designed to fit into existing shells or system footprints, making them a cost-effective solution for increasing capacity or improving performance without major infrastructure changes.
What fluids can Dimpleflo™ handle?
Dimpleflo™ is suitable for virtually any pumpable fluid, including sludges, slurries, steam, process water, chemicals, and fluids with high solid content—up to 80% in some applications.
What temperature and pressure ranges can Dimpleflo™ withstand?
Dimpleflo™ is designed to operate efficiently in extreme conditions, withstanding pressures up to 25 bar and temperatures up to 250°C, depending on the application and configuration.
How do I choose the right heat exchanger profile for my application?
Dimpleflo™ offers shallow, medium, and heavy dimple profiles to match specific process needs. Our technical team can help assess your application and recommend the best configuration based on fluid type, flow rate, and thermal requirements.
Is maintenance required for Dimpleflo™ heat exchangers?
Maintenance is minimal due to the self-cleaning effect of the dimpled tubes, which resist fouling. When needed, cleaning and inspection are straightforward, especially compared to traditional smooth-tube designs.
Do you offer custom solutions or configurations?
Yes. We provide tailored heat exchanger solutions based on your specific process requirements, including custom dimple profiles, materials, and flow configurations.
Where can I get a Dimpleflo™ sample or speak to an expert?
You can request a free tube sample or speak directly with a product specialist by visiting our Contact Us page. We’re here to help you find the right solution for your process.